精密せん断とは?ファインブランキング、シェービング、対向ダイスについて(前編)
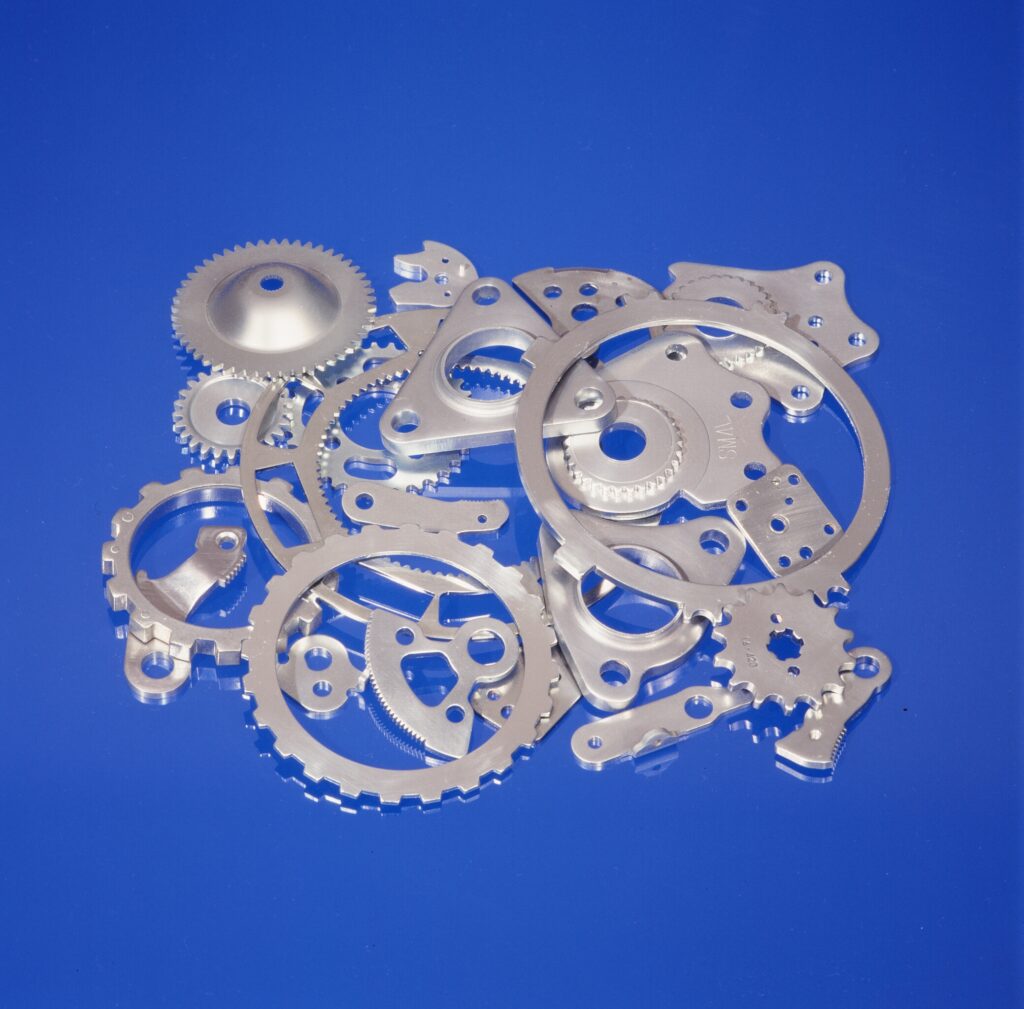
「客先図面に指示されているせん断面がプレス加工でクリアできない。とはいえプレス加工後、2次加工を追加するとコストがかかって利益が出ない」などのお悩みはないでしょうか。そんなとき、精密せん断加工を取り入れることで必要なせん断面が得られる場合があります。この記事では、代表的な精密せん断加工のシェービング、ファインブランキング、対向ダイスについて、加工原理やメリット、デメリットを2回に分けて解説します。
精密せん断加工とは?
精密せん断加工とは、慣用せん断加工で生じる欠陥を抑制して破断面の無い理想に近いせん断面を得るための加工法です。
慣用せん断と精密せん断の分離面の違いを以下に示します。
慣用せん断の分離面
慣用せん断加工はパンチ、ダイにより材料に亀裂を生じさせ分離する脆性破壊加工です。分離面は図のようにダレ、せん断面、破断面とカエリで構成されます。
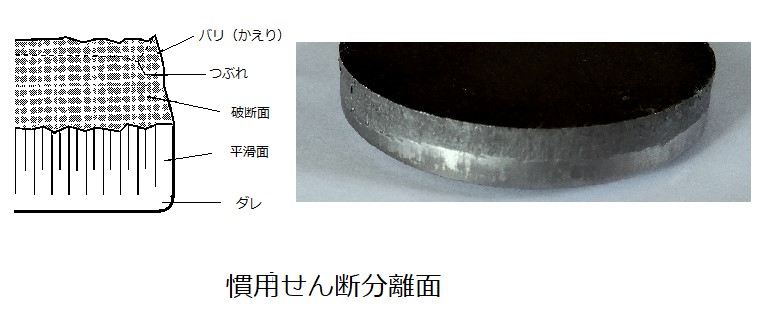
図引用:プレス技術第34巻6号(1995年5月号)P26近藤一義、広田健治
精密せん断の分離面
精密せん断の分離面は小さいダレと平滑なせん断面で構成されます。
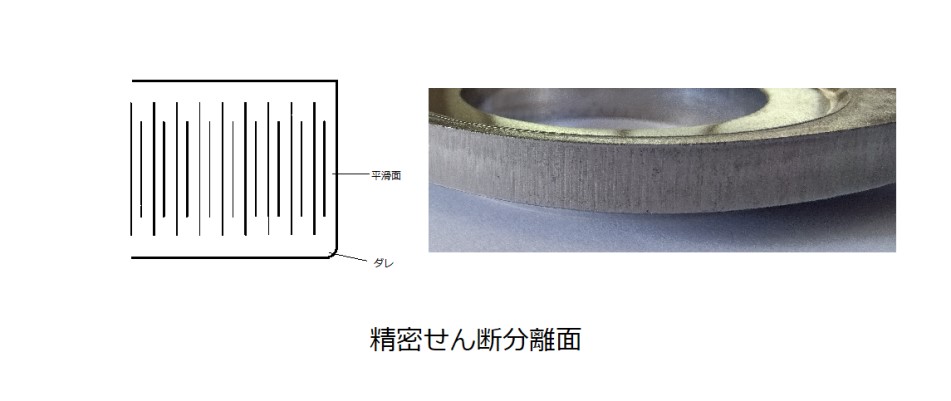
図引用:プレス技術第34巻6号(1995年5月号)P26近藤一義、広田健治
精密せん断加工のメリットとは
寸法精度の良い、平滑なせん断面を持つ部品が生産できるので、慣用せん断加工で必要な2次加工が不要となりコストダウンが可能です。
ファインブランキング加工(以下FB)、慣用せん断加工、切削加工の製造コストと製造工程を比較することにより精密せん断加工のメリットを説明します。
比較部品:オートバイ用ドライブスプロケット 材質SCR420 板厚7.2㎜
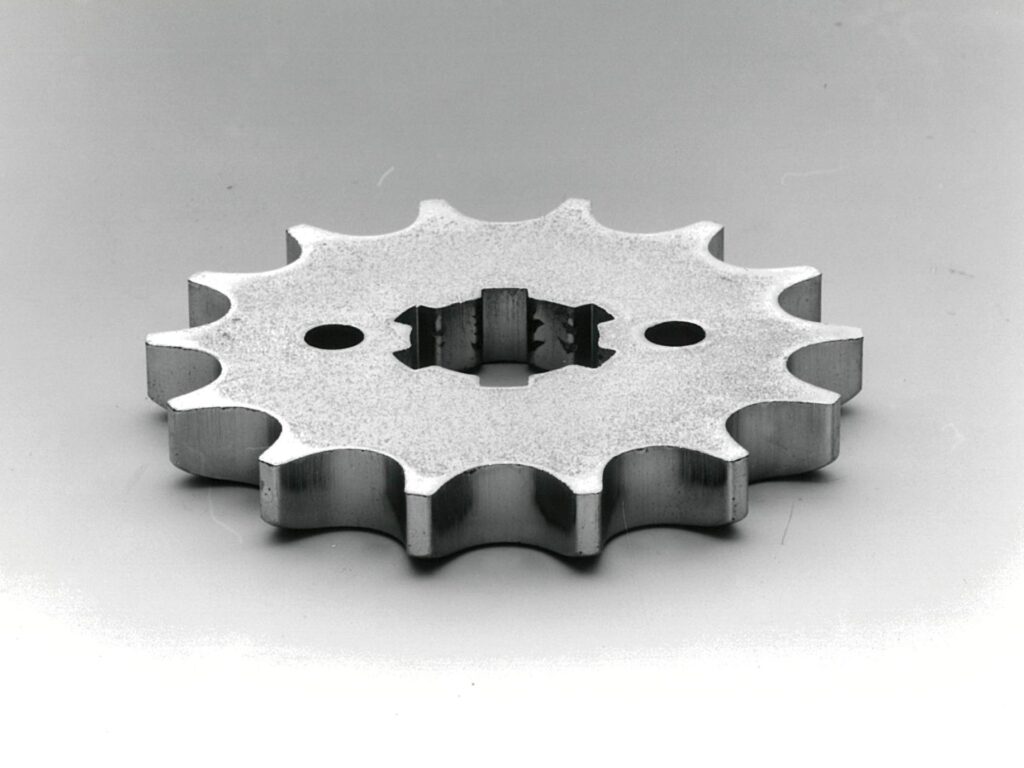
写真はFB加工品
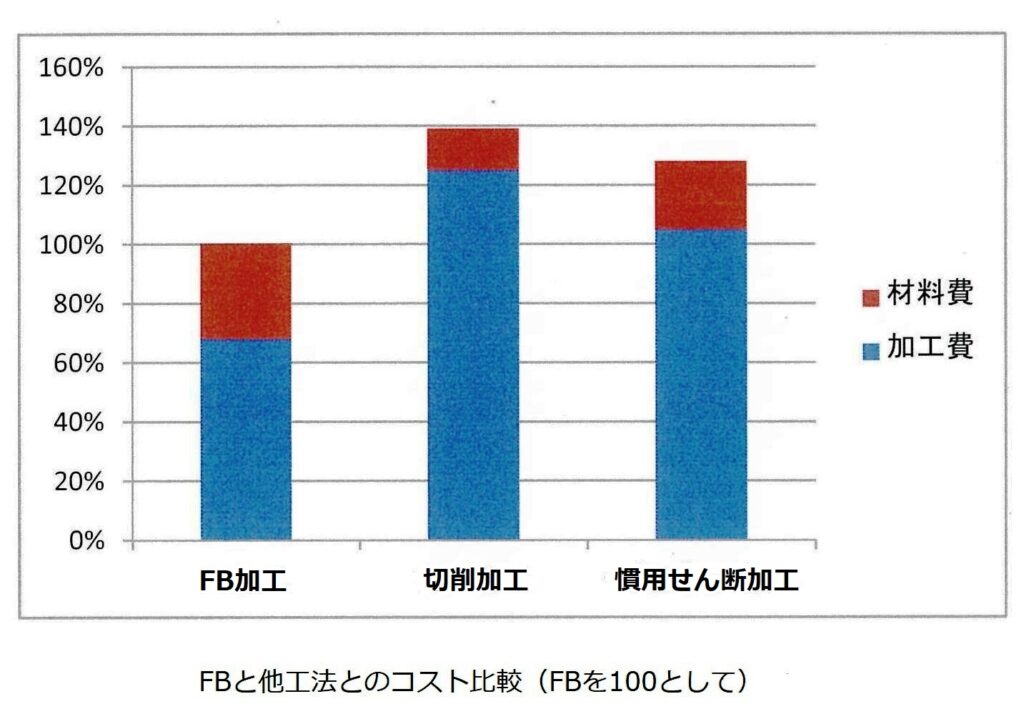
*数値は参考値です。生産数量などにより変動します。
オートバイ用ドライブスプロケットの製造工程
加工方法 | 加工工程 |
FB加工 | FB→バリ取り→タップ→刃先R面旋削→旋削バリ取り→熱処理 |
切削加工 | 丸棒切断→両端面R、外形旋削→タップ下穴旋削→タップ→スプライン下穴旋削→スプライン部ブローチ加工→スプロケット歯形ホブ加工→バリ取り→熱処理 |
慣用せん断加工 | 内外径抜→両端面R、外形旋削→タップ下穴旋削→タップ→スプライン部ブローチ→スプロケット歯形ホブ加工→バリ取り→熱処理 |
FB加工は材料歩留まりが悪いこととFB加工用材を使用するために材料費は高額となります。一方、加工費は外形旋削、ブローチ加工、ホブ加工が省略できるため大幅なコスト削減ができます。また、直接の製造原価のほか、工程の短縮ができるので工程間の在庫削減や、物量費、管理費の削減も可能となります。精密せん断加工の代表的工法であるFBは、ドライブスプロケットの製造において最適な加工法と言えます。
精密せん断の種類
精密せん断加工には、切削機構で平滑なせん断面を得る方法と、圧縮力の負荷により材料の塑性変形能を高め亀裂を防ぐ2つの方法があります。シェービング法が前者に、FB法と仕上げ抜き法が後者にあたります。対向ダイス法は最終分離をFB的に行うため2つの工法を組み合わせた加工法となります。
シェービング法(以下SV)
SVは、慣用せん断で生じる凹凸を切削機構で取りのぞき、プレス加工により平滑で高精度な仕上面を得る加工法です。
SVの原理
切削加工で平滑な加工面が得られる理由は、工具刃先付近に生じるクラックの成長方向が加工面より外側を向き、製品側に達するクラックが発生しないからです。
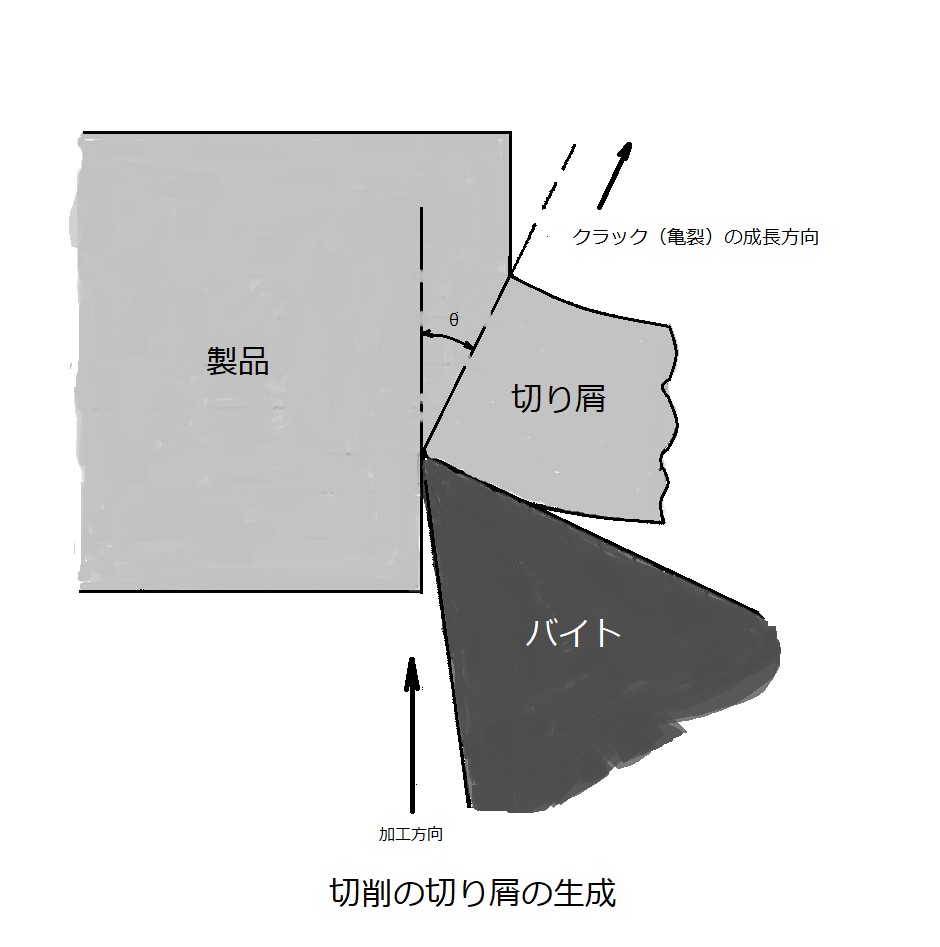
切削の切り屑の生成
通常のせん断加工では、パンチ刃先とダイ刃先を結ぶ領域にせん断変形が生じますが、材料の取り代を少なくするとせん断変形はダイと材料の自由面側に生じます。プレスSVではこの機構を利用し、切削加工と同様にクラックを切り屑側に向けることにより製品側にクラックが発生しないようにしています。加工終期では、せん断抵抗が減少するのでパンチとダイに沿ってせん断変形するほうが抵抗は少なくなります。パンチ、ダイを結ぶ領域にせん断変形が集中して通常のせん断加工と同様の変形機構となるので、SVの最終分離面は破断面となります。

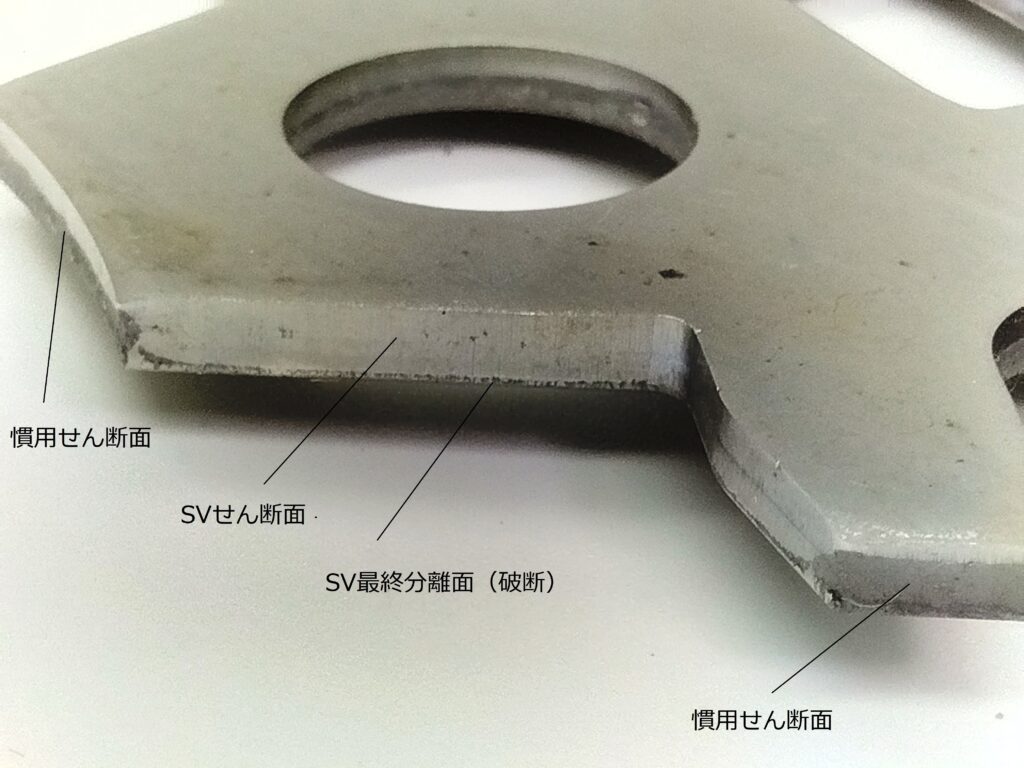
SV加工面 SHP440 t=3.6㎜ T/Fプレス加工 SV1回
SVの加工条件
SVの取り代は材料板厚の5~10%程度ですが、鋼種により取り代は異なります。軟鋼で5%、硬鋼は8~10%、黄銅で10%程度が目安となります。1回のSVで不十分な時は取り代を変え2回、3回とSVを繰り返すこともあります。加工速度もSVに大きな影響を及ぼします。加工速度7m/sec以上の高速SVでは、極めて良好なSV面が得られることも報告されています。FB順送型にSV工程を組み込む場合は、FBプレスの加工速度が遅い(3~70㎜/sec)ため金型に特別な工夫が必要となります。
参考:SVの取り代(1回仕上げ)
ブランク厚さ | 軟鋼 | 半硬鋼 | 硬鋼 | 洋白 | 黄銅 |
1.2㎜ | 0.06㎜ | 0.08㎜ | 0.10㎜ | 0.13㎜ | 0.13 |
1.6 | 0.08 | 0.10 | 0.13 | 0.15 | 0.15 |
2.0 | 0.09 | 0.13 | 0.15~0.18 | 0.18 | 0.18 |
2.4 | 0.10 | 0.15 | 0.18~0.20 | 0.20 | 0.20 |
2.8 | 0.13 | 0.18 | 0.23~0.28 | 0.25 | 0.25 |
3.2 | 0.8 | 0.23 | 0.30~0.36 | 0.36 | 0.36 |
引用:プレス技術第29巻12号P46新加工データブック青木勇
参考:SVの回数
製品輪郭の性質 | SVの回数 | |
板厚3㎜以下 | 板厚3㎜以上 | |
直線・なだらかな曲線 | 1 | 2 |
鋭角のある輪郭 | 2 | 3~4 |
引用:プレス技術第29巻12号P46新加工データブック青木勇
*数値は参考値となります。製品形状、要求品質などにより取り代やSV回数を変えることもあります。
FB順送型のSVレイアウト 材質S45C 板厚 6.0㎜
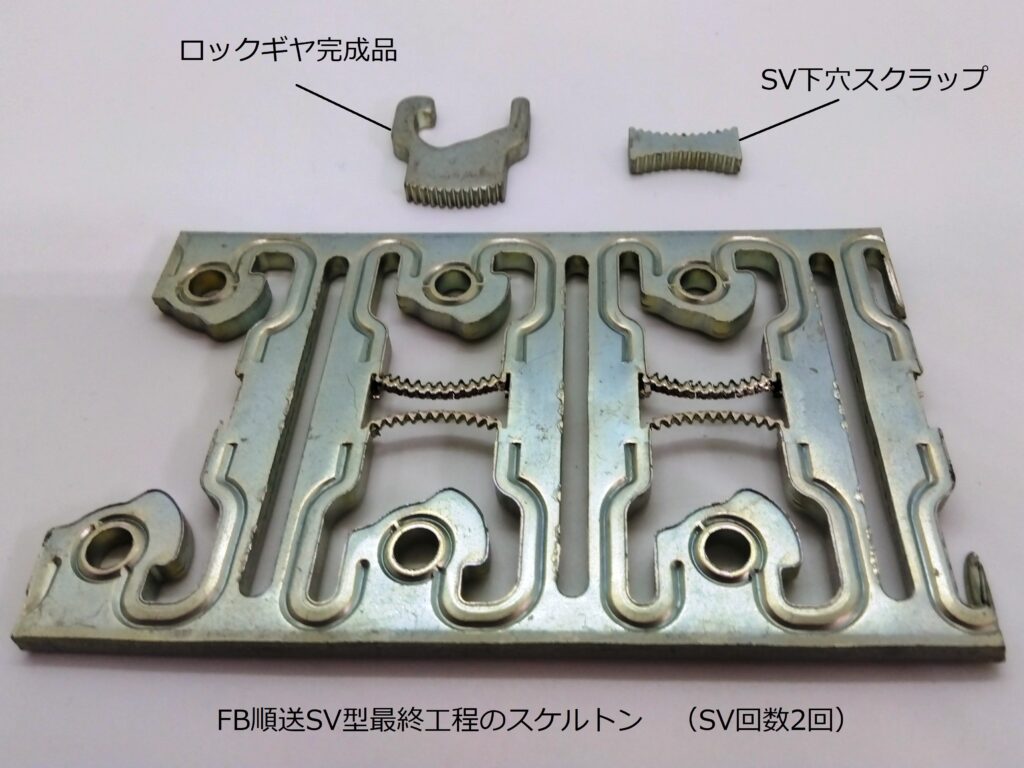
SVの精度
SV製品の精度はすべての点で慣用せん断法と比較し優れています。とりわけ抜ダレは少なく、FBと比較しても極めて小さくなります。
参考:SVの精度
板 厚 | 精 度 (㎜) |
1㎜以下 | ±0.01~0.015 |
1~3㎜ | ±0.025~0.03 |
3~5㎜ | ±0.035~0.04 |
引用:プレス技術第29巻12号P46新加工データブック青木勇
*高精度な金型とプレスを使用し、より高精度の部品を製造している例も数多くあります。
SVのメリット
- 高額な専用プレス機を用いることなく平滑なせん断面が得られる
- 材料を拘束する圧力を使わないため金型構造が簡単
- 切削機構を使うため加工力が少なくダレが極小となる
SVのデメリット
- 加工が2工程以上必要
- サン幅や取り代の影響が大きく出る加工法のため高精度なブランクが必要
- 加工後期での亀裂分離を遅らせるためにクリアランス少ない高精度・高剛性な金型が必要
- クリアランスの少ない金型を使用するため金型の消耗が激しい
- 切刃の摩耗がせん断面に影響を与えるため金型のメンテナンスが頻繁になる
- ひも状につながったスクラップが発生するため金型に付着し製品に圧痕を付ける
SVのデメリット解消
金型の維持管理が難しいSVですが耐摩耗性の高い型材の開発、表面処理技術の向上・高精度な金型・高剛性の精密プレスの登場と相まって、金型の消耗をかなり抑制することが可能となっています。またSVスクラップ残りは金型のラップと表面処理による離型性の向上やレイアウトの工夫などで対策します。
T/F型でのSVスクラップ せん断面不要箇所の取り代を大きくし、重りとした例
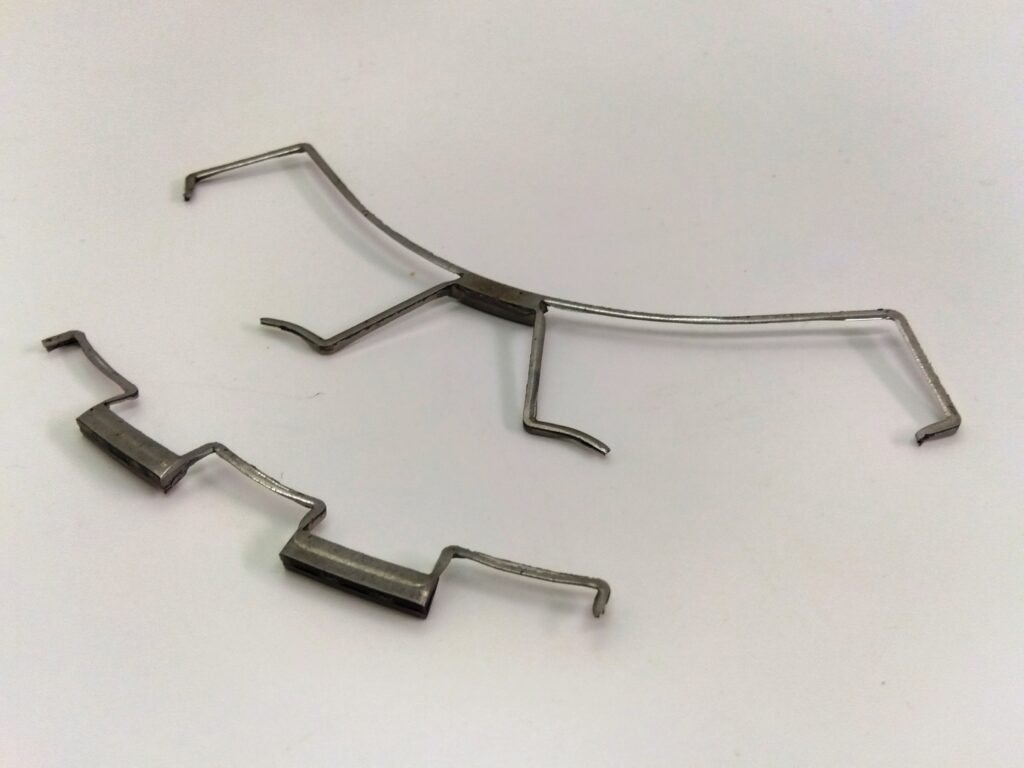
順送型でのSVスクラップ 通常せん断のスクラップにSVスクラップをつなげた例
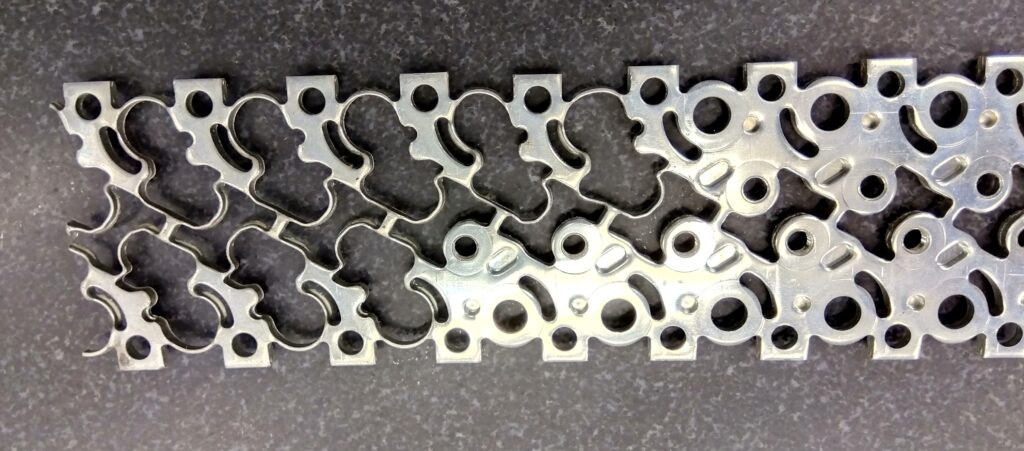
SVの高度な活用
2000年代に入るとサーボプレスや精密成形プレスの登場と相まって、FBの代替としてSVの高度な活用が増えています。順送型やTF型を使用し、板金加工や冷間鍛造にSVを組み合わせて、平滑なせん断面を持つ立体的な形状の板鍛造部品が数多く生産されるようになっています。
不二工機製造(FS WORKS)で設計・製作したSV工程を含む金型の事例
順送型
製品名 ブラケット
被加工材:S45C 板厚4.6㎜
鍛圧部公差:4.4±0.03、穴径:Φ10.15±0.08、座グリ穴径・深さ:Φ11±0.1、2.8±0.1、輪郭度:0.3以下、外周がSVのせん断面
使用プレス機 アイダUL300 工程 アイドル工程を含む22工程順送
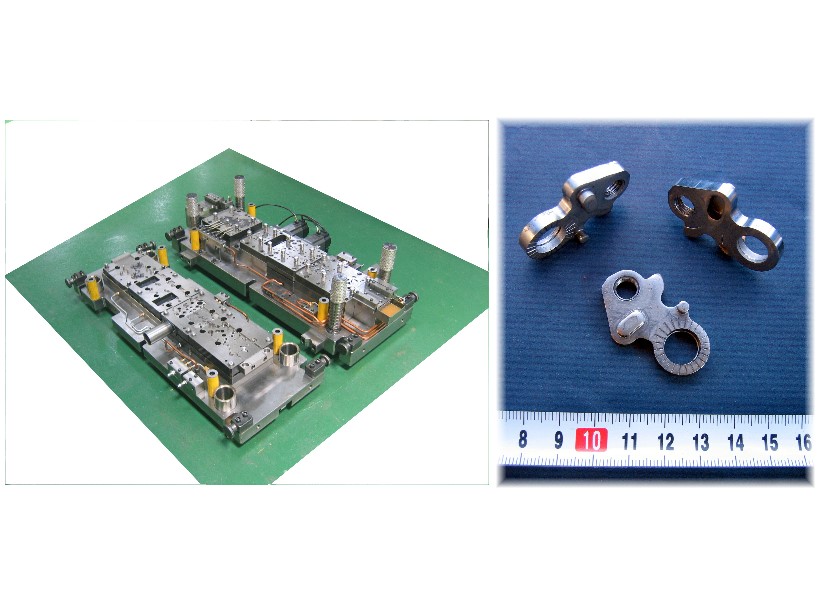
FB順送型
製品名 セクターギヤ、ロックギヤ
被加工材:SCM415 板厚4.5㎜ 外周と孔は100%せん断面 外周ラチェット歯形はSV2工程で加工、通常のFB加工と比較しダレ量は3/1以下
使用プレス FB650t
工程 SV2工程を含む3工程順送型ダイフローティング式
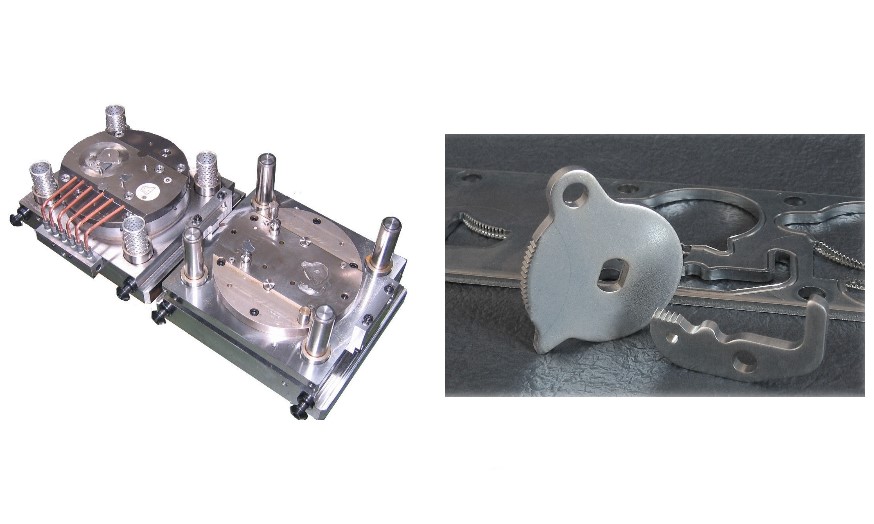
仕上げ抜き法
一般プレスで平滑なせん断面を得る工法です。ゼロクリアランスで切刃に丸みをつけた金型を用いて亀裂の発生を防止します。
仕上げ抜きの原理
仕上げ抜きは、切刃にRを付け刃先近傍に圧縮応力を発生させるとともにパンチ、ダイのクリアランスをほぼゼロとして亀裂の会合を遅らせることにより平滑なせん断面を得る工法です。打ち抜きではダイ側に、穴あけではパンチ側にRまたは面取りを施します。
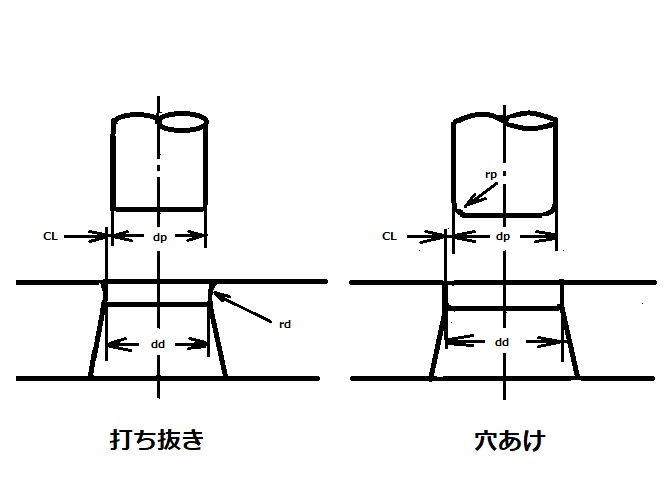
CL | rd |
0.02 | ~0.25 |
0.05 | 0.25~0.5 |
1.0. | 0.5~ |
参考:軟鋼板で破断の発生しない条件(板厚2.0㎜~4.5㎜)
引用:プレス技術第29巻12号P47新加工データブック青木勇
仕上げ抜きのメリット
・特別なプレスや金型を必要としない
仕上げ抜きのデメリット
・材料が高延性材で打ち抜き形状が比較的単純なものに限定される
・ダレ・湾曲が大きい
仕上げ抜きの寸法精度
仕上げ抜きの製品精度は金型のクリアランスと切刃のRの大きさで変わってきます。切刃のRが大きいほどダレ、湾曲が大きくなるのでRは必要最小限に抑える必要があります。
FB法
FBは、スイス人のフリッツ・シース・フォーラ―氏によって1920年代に開発された技術で、100年以上の長い歴史を持っています。
FBの原理
一般プレス加工が一軸の脆性破壊によるせん断分離に対し、FBは3軸の塑性変形によるせん断加工となります。FBでは、静水圧効果を得るためV型環状突起で被加工材を拘束し上下から圧力を加えながら打ち抜きます。加工部近傍に集中的に圧力が加わることで静水圧効果が得られ、全面が平滑にせん断されます。
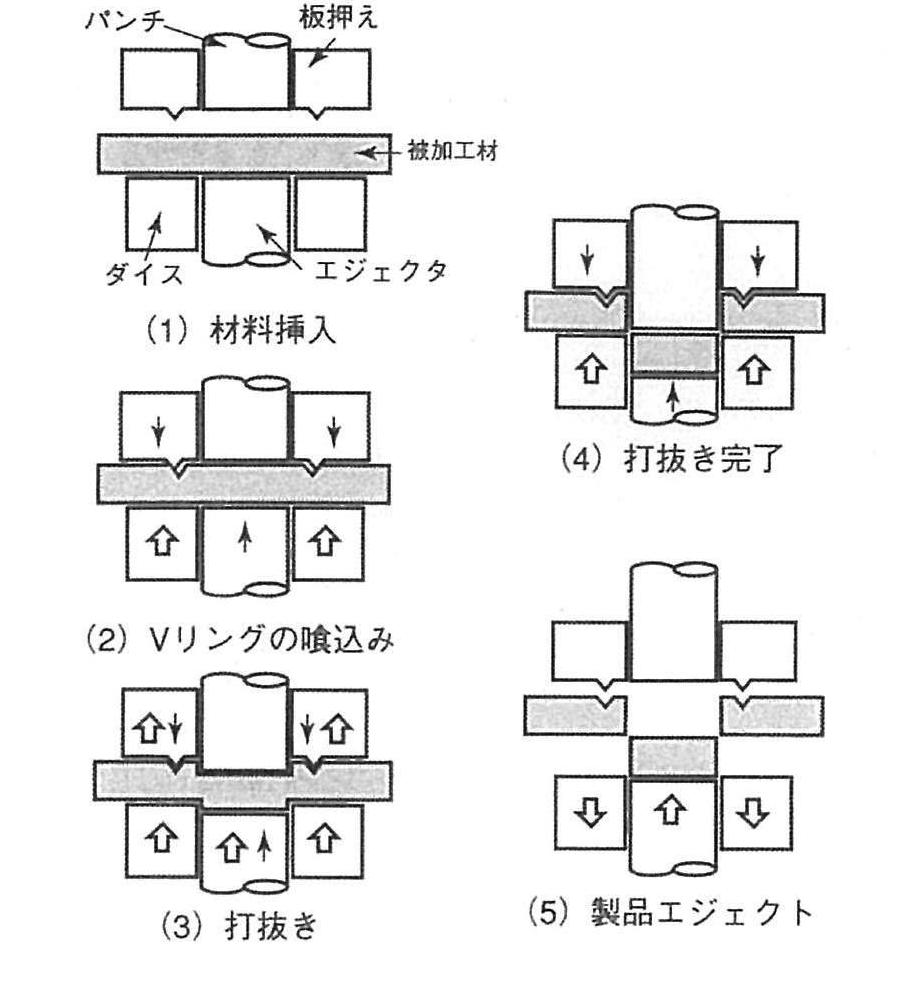
FBの加工工程
FBの精度、加工限界、メリット、デメリット、事例は以下の記事をご参照ください。
次回は対向ダイスせん断法について解説します。
この記事をシェアする
この記事を書いた人
- 2025年7月9日NEWS創立記念日
- 2025年7月2日NEWS夏季休業のお知らせ
- 2025年6月9日NEWS新装置「マイクロデポ」導入のお知らせ
- 2025年5月30日ブログお客様から見た不二工機製造(FS WORKS)