板鍛造とは?板金や冷間鍛造との違いや定義、メリット、製品事例を紹介
-1024x824.jpg)
「板鍛造(読み方:いたたんぞう)」とは、「板金(読み方:ばんきん)」と「鍛造(読み方:たんぞう)」双方のメリットを組み合わせた工法で、板厚変化をともなう立体形状をプレス加工のみで実現する技術です。
打ち抜きや曲げといった単純なプレス生産の海外移管が進むとともに、国内ではより高付加価値な加工が求められるようになったことで、2000年代より導入が進みました。
現場でよく聞く板鍛造ですが、実際にはどのような加工方法なのか?板鍛造を用いてどのような製品を成形できるのか?と疑問に思う方もいらっしゃると思います。
そこで、この記事では、板鍛造の定義から冷間鍛造やプレス加工との違い、金型製作のポイントまでを解説し、製作例を写真付きで紹介していきます。
目次
板鍛造とは「板金」と「鍛造」を組み合わせた加工技術
_不二工機製造(FS-WORKS)-1024x440.jpg)
板鍛造とは、「板金」と「鍛造」を組み合わせた加工技術であり、「いたたんぞう」と読みます。より具体的には、一般的な板金成形の打ち抜き、絞り、曲げ、バーリングに加えて、冷間鍛造の据込み、しごき、押し出しなどの工法を取り入れた複合成形加工法です。
板金工程の一部に鍛造を組み込むことで、板厚のある素材から立体的な形状を一度に成形できるのが特長です。
略称には「FCF(Flow Control Forming in Sheet Metal)工法」や「CFP(Cold Forging Progressive)工法」などがありますが、板鍛造を手掛けるメーカー各社で異なる略称を用いており、通称は決まっていません。
製造業において板鍛造の技術が注目されるようになった背景
板鍛造は日本生まれの新技術です。板鍛造の技術が生まれたのは、より高付加価値なプレス加工が求められるようになったことがきっかけでした。
1990年代、従来のプレス加工で行ってきた打ち抜きや曲げといった単純な部品加工は、海外への移管が進みました。すると、国内では高付加価値なプレス加工が求められるようになり、異なる工法を組み合わせることで複雑な形状を一体成形してしまおうという発想が生まれます。
結果として、オールプレスで立体形状を成形できる板鍛造の技術が注目されるようになります。金型の材料開発、表面処理の技術の向上、サーボプレス機(加圧条件を任意に設定できるプレス機)や精密成形プレス機の登場と相まって、2000年代に板鍛造が普及していきました。
そもそも板金プレス加工と冷間鍛造加工とは?それぞれの違い
ところで、そもそも板金と鍛造の違いは何でしょうか?板鍛造の理解を深めるために、それぞれの工法について解説します。
板金プレス加工
板金は「ばんきん」と読みます。板鍛造でいう板金とは広義のプレス加工を指し、金型を用いて板材から同形状の部品を大量に成形する工法のことをいいます。
-1024x236.jpg)
具体的には、コイル材のような板厚数mmの金属板を送り出し、金型を押し当てて打ち抜きや曲げ、絞りなどを行います。一度に大量の部品を成形でき、1個あたりの生産コストを大幅に安くできるのがメリットです。
冷間鍛造加工
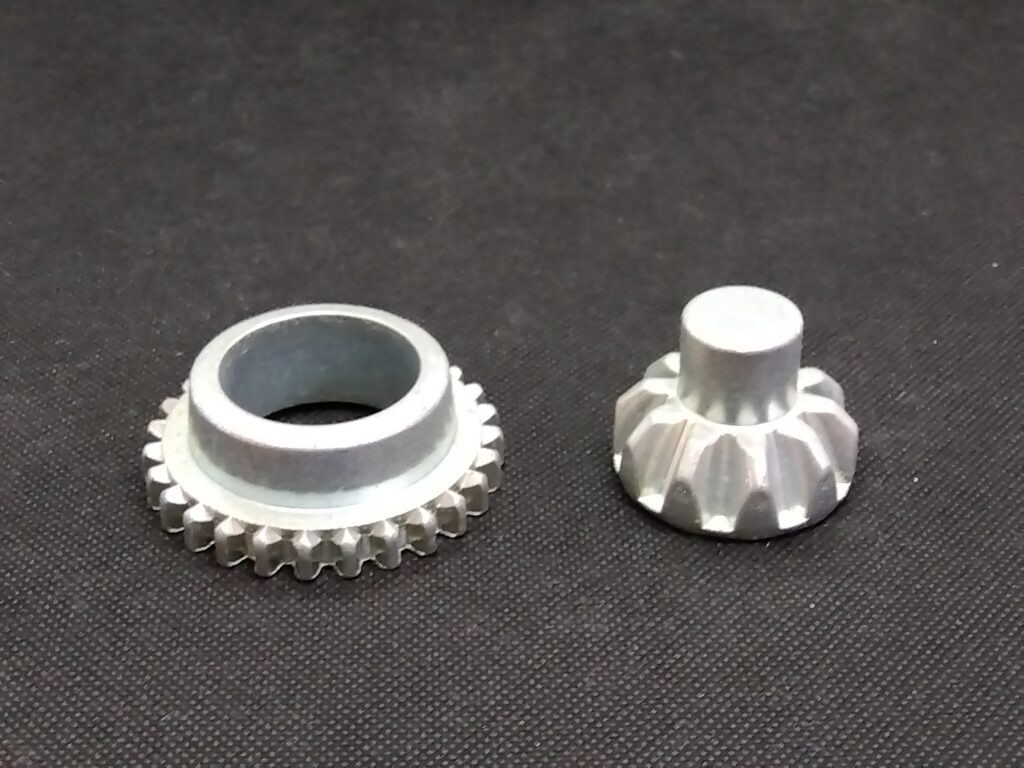
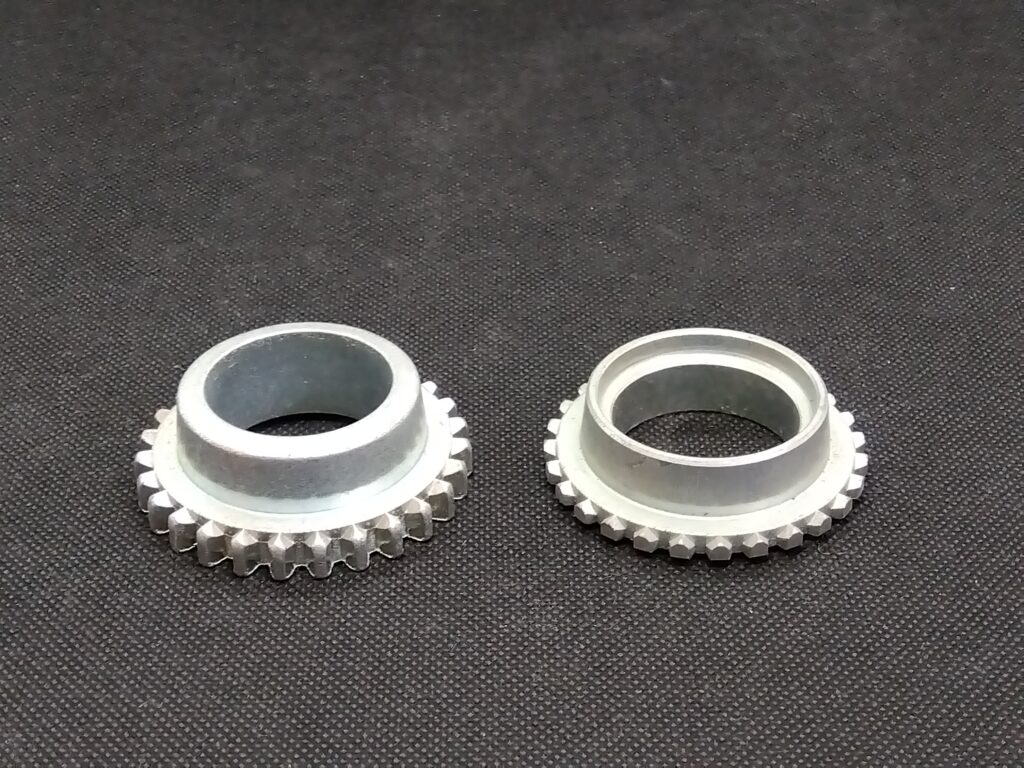
鍛造は、ひと言で表すと、金属を叩いて目的の形状に加工する技術です。打撃・圧縮によりワークである金属が強くなるので、「鍛えて造る=鍛造」と呼ばれています(※)。
※現在ではプレス機と金型を使用する「型鍛造」を指すことが多くなっています。
ワーク全体はもちろん、ワークの一部を変形することも可能です。肉厚なワークや金属塊、丸棒材であっても加工でき、増減肉を容易にします。切削加工に比べて歩留まりや加工スピードが向上するのが特長です。
なかでも、ワークを常温のまま加工する鍛造の方法を冷間鍛造(読み方:れいかんたんぞう)と呼び、板鍛造に用いられるのは冷間鍛造加工になります。
冷間鍛造と熱間鍛造の違い
冷間鍛造と熱間鍛造の違いは、ワークを常温まま加工するか、ワークを高温度域(焼く1150~1250℃)に過熱して加工するかです。
冷間鍛造では、ワークを常温で加工します。寸法・形状精度がよく、表面の仕上がりもきれいで高精度な製品加工が可能です。ただし材料の流れが悪く変形抵抗が高いので、成形できる形状に限界があり成形時には大きな力が必要です。
熱間鍛造では、高温度域となる約1150~1250度域までワークを加熱して成形します。鉄を鍛えて刀を作るイメージが分かりやすいかもしれません。加熱によりワークの変形能が高まるので、複雑形状や大物の成形に向きます。ただし、熱による膨張、鍛造による反りやスケールが発生するため、寸法精度や表面性状は冷間鍛造に比べ劣ります。
板金プレス加工と冷間鍛造の違い
板金プレス加工と冷間鍛造の違いは、幅広で薄い板材から平面的な形状を成形するか、肉厚な素材から立体的な形状を作りだすかです。
板金プレス加工で用いられるのは、「ブランク」や「コイル材」と呼ばれる薄くて幅広の板材です。金型を押しあて形を転写したり、曲げ、打ち抜き、絞りといった工程により目的の形状を作り出します。比較的単純な加工を連続的に行いますので、大量の部品を低コストで作ることに向いています。

一方の冷間鍛造では、「ビレット」と呼ばれる厚みのある素材から成形を行います。ワークを金型で挟みこみ、型に沿った肉厚で立体的な形状を作りだします。さらに、成形された部品は高精度でネットシェイプやニアネットシェイプ(完成品に近い状態)となります。
板鍛造と板金プレス加工の違い
-1024x768.jpg)
-1024x768.jpg)
板鍛造と板金プレス加工の違いは、板鍛造は板金プレス加工の一部に局部的に鍛造の工程が組み込まれていることです。一般的な板金成形の打ち抜き、絞り、曲げ、バーリングなどに、冷間鍛造による据込み、しごき、押し出しなどを加えた複合成形が可能です。
板鍛造のメリットは立体形状の肉厚部品を高精度かつ低コストで製造できること
板鍛造のメリットは、立体形状の肉厚部品を最低限の工程で大量に成形できることです。成形品はネットシェイプやニアネットシェイプとなり、高精度と低コストが実現します。
板金では部品は軽量に仕上げやすく、鍛造加工では強度が必要な部分を増肉することが可能です。つまり板鍛造により、強度と軽量性を兼ね備えた部品をプレスで一体成形することが可能となり、材料歩留まりも向上します。
とくに、ほぼ100%のせん断面をプレス加工で得られる「ファインブランキング(以下、FB)」を用いることで、優れた平面度・直角度を有する高精度な板鍛造部品の加工が可能になります。
-1024x812.jpg)
-1024x768.jpg)
板鍛造の産業への応用例と板鍛造への工法転換による効果の事例
実際に板鍛造はどのような産業・製品に応用がされているでしょうか?また、板鍛造への工法転換によって、どのような効果が期待できるでしょうか?
板鍛造のメリットや製作できる製品群のイメージを持っていただけるように、以下、不二工機製造(FS WORKS)の事例をもとに解説します。
- 産業への板鍛造の応用例
- 板鍛造への工法転換による効果の事例
1.板鍛造の産業への応用例
板鍛造は、とくに自動車部品に多く応用されています。軽量化、高強度、耐久性の向上に寄与し、中厚材の複雑形状加工に有効であるためです。
たとえば、歯車構造をもつギヤ部品や、フランジのように一部を増肉する部品などの製造によく用いられています。自動車産業などへの具体的な応用例を紹介します。
自転車リアーデイレーラー用ブラケット
-880x1024.jpg)
材質:S45C、板厚:4.6mm
鍛圧部交差:4.4±0.03、穴径:Φ10.15±0.08、座グリ穴径・深さ:Φ11±0.1・2.8±0.1、輪郭度0.3:以下
レイアウト:22工程
工程の特長
-1024x768.jpg)
減厚、エンボス、カウンターシンク(座グリ)加工のある複合成形を実現。金型のクリアランスはFBと同等(板厚の0.5%)に設定し、製品外周は100%のせん断面を得ました。
プレス加工時にタップ加工を行うためサーボモーター駆動のタップユニットを組み込んでいます。外形打ち抜きでタップ穴の変形および座グリ穴周りのダレを最小に抑えるため、部分的にシェービング加工を行っています。シェービング加工で材料逃げによる破断面の発生を抑えるため、板押さえプレートに材料を拘束するガイドを設けました。
金型の特長
-1024x768.jpg)
- 4つのブロックで構成し、第2、4ブロックでロッキング機構付きの油圧クッションを使用
- 第2ブロックはダイ可動、第4ブロックはFBの動作
- 鍛圧、カウンターシンク穴パンチ、ダイ、外抜きダイに超硬を使用
- 主要成形部品やガイド類にはTicn処理を施している
2.板鍛造への工法転換による効果の事例
粉末冶金で成形していた部品や、溶接・圧入などを要していた部品を板鍛造に変更することで一体成形が可能となり、大幅なコスト削減に繋がった事例を紹介します。
つぶし加工例:シートリクライナー用ロックギヤ
-1024x768.jpg)
-1024x768.jpg)
工法変更により大きなコストダウンを実現しました。
材質:S45C
板厚:6.0㎜
ギヤモジュール:0.55
特長:つぶしによりギヤとカム面を成形
従来工程:プレスブランク加工→冷間鍛造→トリム→二面幅切削→熱処理→ショット
改善後:FB順送(8工程)加工→バレル→熱処理→ショット
増肉例:4輪ブレーキ用ブラケット
増肉加工_不二工機製造(FSWORKS)-1024x556.jpg)
FB順送加工により、製品上必要な部分のみ増肉し、材料費を低減、軽量化を実現しました。
材質:SAPH440
板厚:6.0mm
穴周りに2mmの増肉
レイアウト:4工程
エンボス成形例:ドアーロック用ラッチ、ラチェット
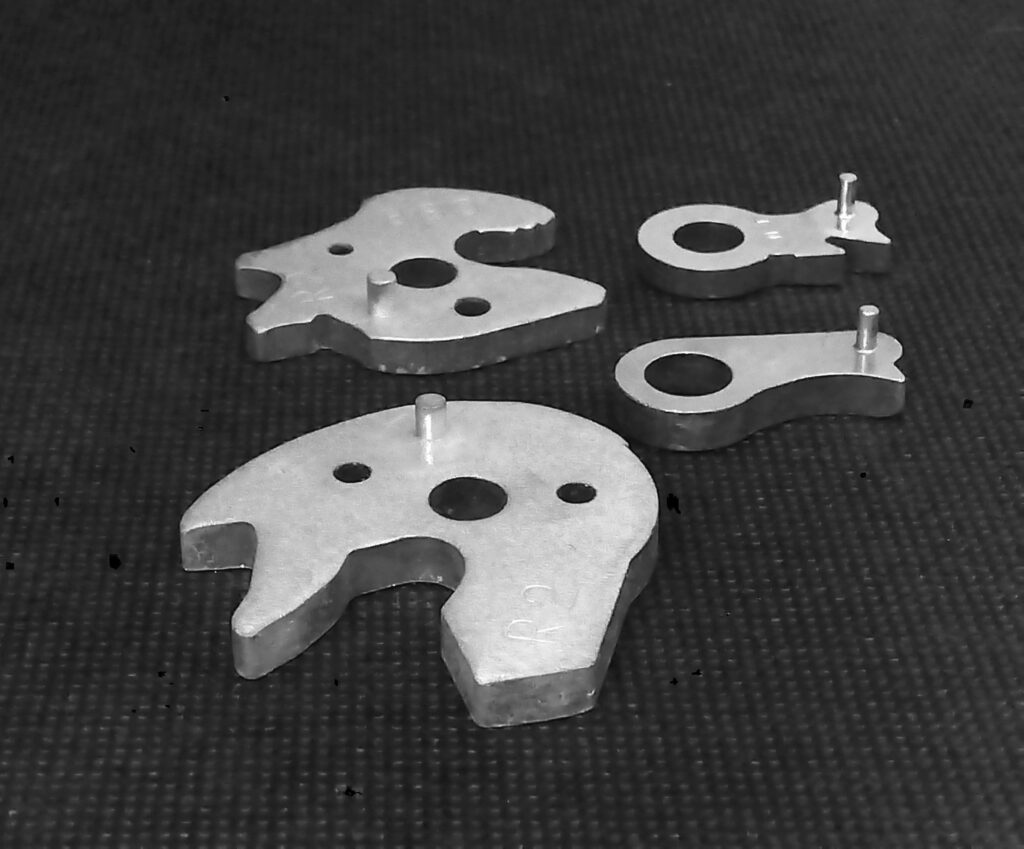
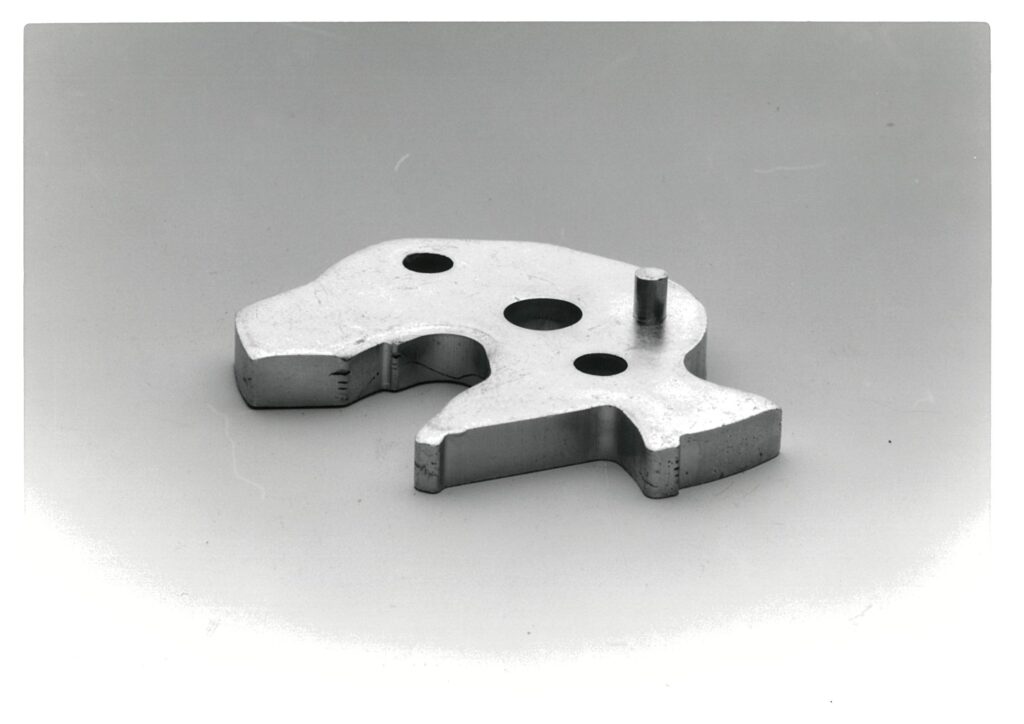
前方押し出しによりエンボスを一体成形することで、ピンの製作と圧入の工程を不要にしました。板鍛造により材料のファイバーフローが切断されずに部品の強度が上がり、ピンが抜けてしまう製品リスクも解消されました。
3つの独立した油圧源を持つFBプレスを使用すればエンボス成形は比較的容易なため、FB+エンボス成形はFB加工普及の初期段階【1960年代】より実施されています。
ツブシにより内側のギヤを成形:2段ギヤ
-1024x768.jpg)
材質:SAPH440
板厚:6.0㎜
ギヤ歯先円形:外φ26±0.02、内φ23±0.02
特長:FB順送型で加工
板鍛造の金型設計におけるポイント6つ
板鍛造では金型に大きな荷重がかかるため、金型の破損が多くなります。設計段階でさまざまな因子をよく検討しなければ、金型の内部にクラックが発生し、気付かず不良品を流してしまうようなトラブルにつながってしまいます。
では、どうすれば板鍛造における高精度な金型を実現できるのでしょうか?以下にポイントを6つ紹介します。
- 変形抵抗、加工力、塑性流動を考慮する
- ワークと加工条件に応じ、型材の材質とサイズを選定する
- 新生面の出現とワークの発熱を計算し、潤滑油で対策を講じる
- 製品の要求精度に応じてレイアウト(加工工程)を組む
- 金型の表面粗さを上げ、摩擦係数を小さく抑える
- 工程の最後にダレの少ない全域せん断を実現する
1.変形抵抗、加工力、塑性流動を計算する
.png)
板鍛造の金型設計において、鍛造工程の設計が重要であり難しいポイントとなります。
そのため、CAE(シミュレーション解析ソフト)で事前に材料の挙動を解析し、成形応力を低減する対策を取っておくことが重要です。解析をもとにスリットや捨て軸・捨て穴を適正に配置することにより、トライ後の金型の改修を最小限に抑えることができます。
「初歩から学ぶ鍛造加工」湯川伸樹-Nobuki-YUKAWAより.jpg)
加工時のワークの変形は金型により拘束を受けますが、プレス機の荷重が不足すると金型内に欠肉が生じてしまいます。だからといって荷重を上げすぎると、変形抵抗が高くなりすぎて金型への負担が大きくなります。捨て軸、捨て穴を設けることにより成形応力を減らし、肉の充填も促進されます。
2.ワークと加工条件に応じ、型材の材質とサイズを選定する
ワークの素材と加工条件などに応じ、金型の材料も適切な材質とサイズを選定する必要があります。とくに冷間鍛造工程では成形応力は100~250㎏/㎜²になり、この応力の繰り返しに耐えるよう十分な剛性と強度を持たせなければいけません。
たとえば、つぶし工程における金型の剛性不足は、つぶし量の不足やつぶし量のバラツキつながります。設計段階で適切な金型材料を選定するとともに、バックアッププレート類も十分な厚みを取ることが重要となります。
冷間ダイス鋼、ハイス鋼、粉末ハイス鋼、超硬合金などが良く用いられますが、超硬合金の使用ではインサート構造として、超硬で製作した刃具部品を組み込むような形の対応も必要となります。
3.新生面の出現とワークの発熱を考慮し、潤滑油で対策を講じる
鍛造におけるトライポロジーの最前線.jpg)
板鍛造工程では、ワークが金型に押しつけられ変形・変質することによって、金型と凝着してしまう場合があります。そこで、潤滑油を用いた対策が欠かせません。
冷間鍛造において変形量の多い加工ではボンデ潤滑が用いられていますが、コイル材からの板鍛造では加工上、潤滑油を使用します。
金型の接触やせん断などで摩擦が生じると、金属の表面に高い化学活性を持つ「新生面」が露出します。金属の新生面には多くの化合物が化学的に吸着しやすく、金型と凝着を起こしてしまうことがあります。あるいは、加圧や塑性変形によってワークが発熱することによっても、金型との凝着が起きやすくなります。新生面の出現とワークの発熱を考慮し、適切な潤滑油を選定をしましょう。
順送型での板鍛造加工では、下流側で潤滑油切れを起こさないよう金型内潤滑機構やオイルポケットを設けておくことが重要です。また、潤滑油が密閉されると思わぬトラブルが発生するので、油逃がしも必要となります。
4.製品の要求精度に応じてレイアウトを組む
板鍛造の金型ではレイアウト(加工工程)も非常に重要です。たとえば、プレスの荷重中心のあるところに極力、冷間鍛造工程を設けるようにするのが基本となります。あるいは、製品の精度に影響のない工程は前工程に持っていき、精度に関係する工程は後工程に持っていきます。
_不二工機製造(FS-WORKS)-1024x749.jpg)
上記は、フランジ12工程板鍛造順送型 (10000kN順送プレス用)の製作例です。荷重バランスをとるため、加工5工程のほかアイドル7工程を採用しました。
工程:スリット・下穴抜き→第1成形→第2成形・センター孔抜→押出しせん断→ヌキ落とし
-1024x542.jpg)
-1024x614.jpg)
荷重バランスや材料の変形を考えながら、最適なレイアウトを組んでいくことが重要です。
5.金型の表面粗さを低減し、摩擦係数を小さく抑える

金型と素材表面の摩擦係数は変形応力に影響を与える要素のため、なるべく最小限に抑えます。そこで、金型部品の表面粗さを低減することが重要です。ラッピングで鏡面仕上げをほどこした後、必要に応じてコーティングを行います。このような表面処理により、金型の耐久性、離型性、防汚性を大きく向上させることができます。
6.工程の最後にダレの少ない全域せん断を実現する
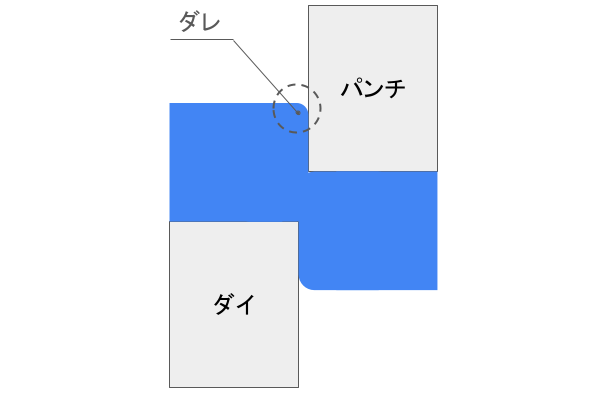
最終的にワークから部品を切り離す「せん断」の工程で、ダレを抑制する工夫が求められます。
ダレの少ない全域せん断を実現するためには、適切なクリアランスを設定し均一なクリアランスを保つことが重要です。一方で、そもそもクリアランスの存在がダレの原因になることにも注意が必要です。
そこで、ワークに上下からの圧力をかけて金属の塑性変形能を高めることで、ほぼ100%のせん断面を得られるFBの工法を用いることが有効です。加工スピードは一般的な板金プレスより落ちますが、後加工が不要になるので結果としてコスト削減を実現できる場合があります。
以下「高精度な自動車部品 金型の要件とは?」の記事において、プレス製品の精度を決めるクリアランスの設定のポイントについて解説しています。あわせてご参照ください。
板鍛造における最新の技術と動向
.png)
板鍛造は2000年代に日本国内で注目され、実際に普及していったのは2015年頃からです。今もなお多くの可能性を秘めた技術であり、板鍛造用の金型を設計・製作できるメーカーもまだまだ少ないといえます。
板鍛造においては材料をどこにどう逃がすかがポイントですが、さまざまな要因が絡むためにその技術を数値化・体系化することは困難です。CAEも進歩していますが、実際にトライしないと金型の評価は難しいのが現状です。
弾性変形を織り込んだCAEソフトを独自開発する動きもありますので、今後はCAEの発展とともに板鍛造金型の設計・製作がしやすくなっていくかもしれません。また、板鍛造への工法転換によるコスト削減効果は非常に高いため、これまで導入されていなかった業界や製品への応用も進んでいくでしょう。
忘れてはならないのは、板鍛造は日本発祥の技術であること。日本メーカーに優位性があるため、海外へのプロモーションも奏功するかもしれません。
板鍛造とは?まとめ
板鍛造とは板金プレス加工に鍛造の工程を組み合わせた加工技術です。板厚変化をともなう立体形状部品をオールプレスで、高精度かつ低コストに製造できます。
板金と鍛造のいいところ採りによって、これまで複数に分かれていた部品を一体化できるなどメリットの大きい工法です。しかしながら、さまざまな要因を考慮しなければならず、金型設計・製作には相応のノウハウが必要となります。
今後はCAEの発展とともに板鍛造金型の設計・製作がしやすくなっていくことが考えられます。また、日本メーカーに優位性のある工法でもあるので、板鍛造の導入や工法転換を積極的に検討していけるとよいでしょう。
不二工機製造(FS WORKS)における板鍛造技術
-849x1024.jpg)
不二工機製造(FS WORKS)では、1966年の創業以来、精度要求の厳しい自動車業界で500型以上の高精度な金型を納めてきました。
プレス加工で破断のない平滑なせん断面を得られるFB金型を主力とし、板鍛造への工法転換でも多くの実績をいただいております。
いずれの型も社内設計標準および客先型仕様に準拠した合理的な設計となっております。図物一致で組み付け精度の高い金型部品および金型をご提供しています。
高精度な板鍛造 金型の製作をご検討の方は、お気軽にお問合せください。
この記事をシェアする
この記事を書いた人
- 2024年3月1日ブログ静岡県浜松市で精密部品の放電加工を受託、電極設計から一貫製作
- 2024年2月29日ブログ三次元測定機をはじめとする万全の品質保証体制、ISO9001・JIS Q 9100にも準拠
- 2024年2月12日ブログ歯車検査とは?主要項目と検査手法、歯車検査を効率化するためのノウハウを解説
- 2024年1月22日ブログ板鍛造とは?板金や冷間鍛造との違いや定義、メリット、製品事例を紹介